NEL RISPETTO DEI CONSUMATORI
BIRAGHI S.P.A. QUALITY DEPARTMENT
Biraghi S.p.A. is a licensed holder of the SGS mark, which has certified the quality of our products and organization in accordance with the UNI EN ISO 9001:2015 standard. The scope of this certification is as follows: “Development, production, aging, portioning, grating, and packaging of cheese. Development, production, and packaging of butter and dairy products derived from milk and whey.”
In addition, our Cavallermaggiore facility has also obtained the prestigious IFS (International Food Standard) and BRC (British Retail Consortium) certifications from the same international certification body.
These certifications serve as a testament to our unwavering commitment to maintaining the highest standards of quality, safety, and hygiene throughout our operations. We continually strive to meet and exceed the expectations of our customers by adhering to internationally recognized quality management systems and undergoing rigorous audits and assessments.
At Biraghi S.p.A., quality is at the forefront of everything we do. We are dedicated to delivering products that not only satisfy but also inspire confidence in our customers.
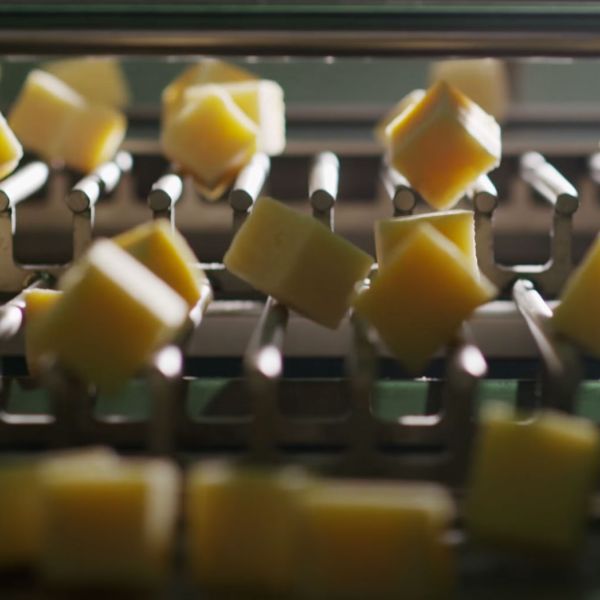
The mission of Biraghi S.p.A. is to consistently provide products and services that fully meet the needs of customers and consumers. The Biraghi S.p.A. Quality Management System ensures that every processing phase is codified to ensure consistent quality over time.
Biraghi offers a dedicated page in the Contact section for product inquiries. Through this tool, customers can reach out to the Biraghi Quality Management System, which is already active and attentive to the needs of our clients. We also extend our services to the final consumers of our products. All suggestions and feedback from consumers are individually recorded, managed with expertise, evaluated as a whole, and used as real opportunities for improvement. Through appropriate recording methodologies, Biraghi ensures systematic traceability of data related to various production processes and statistical analysis of the results obtained. This enables us to achieve controlled and consistent quality over time.
At Biraghi, we are committed to continuous improvement and strive to create a dialogue with our customers and consumers. We value their input and utilize it to enhance our processes and deliver products that consistently meet their expectations.
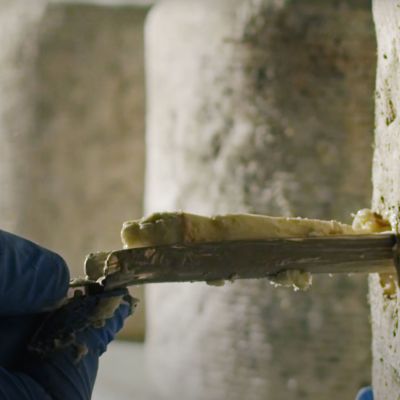
To ensure daily control over its raw materials, particularly milk for cheesemaking, Biraghi S.p.A. possesses a well-equipped in-house analytical facility.
The testing laboratory of Biraghi S.p.A., established in its current operational structure since 1997, carries out comprehensive quality control over the company’s production processes. This includes qualitative testing of milk from individual contributing farms, as well as examining the compositions and characteristics of intermediate and finished products.
The Biraghi laboratory collaborates with qualified partner laboratories for accredited self-control analyses. Analytical reports accredited by Accredia are obtained through microbiological checks on raw materials, intermediate products, and finished goods. Analytical controls also extend to environmental monitoring of the facility’s water, hygiene and sanitation verification of work areas, and research and development activities within the Biraghi domain.
The laboratory employs four operators who work daily, each dedicated to different aspects of sampling and control activities. They utilize cutting-edge, technologically advanced measurement systems that provide precise and reliable results in very short time frames.
The laboratory is equipped with rapid detection systems and charm tests for milk antibiotics, rapid detection and ELISA for aflatoxins in milk, IR systems for determining the chemical-physical characteristics of raw materials, and an electronic nose for organoleptic checks. The laboratory is divided into two operational sectors: chemical-physical-rheological and microbiological sampling. Analytical data is recorded using specialized software for production analyses, enabling detailed processing of the results.
The presence of this advanced in-house analytical facility underscores Biraghi’s commitment to ensuring the highest quality standards and continuous improvement throughout their production processes.
Great importance is placed on customer service at Biraghi S.p.A. The company can provide periodic and punctual control analyses upon customer request for the batches of products they purchase. This analytical support ensures customers’ confidence in the final consumer and regulatory authorities. The company is also available to customers for any consultation or discussion regarding the purchased products, technical matters, and food industry standards. In recent years, the food sector has seen the development of new concepts and approaches to achieve “Total Quality” and ensure the consumer’s health and food safety. This is reflected in the new EC Regulations that constitute the so-called “Hygiene Package,” including regulations 852/2004 on food hygiene, 853/2004 on hygiene for animal-derived products, and 2073/2005 and 1441/2007, which establish new microbiological criteria and limits for various food matrices.
In the context of food safety, it is crucial for producers to have detailed knowledge of their products’ characteristics, emphasizing the importance of scientifically defining the shelf-life parameter. The quality department has been working on studying and verifying the commercial life of products based on a detailed characterization of each of them.
Regarding research and development, the laboratory and the quality office dedicate a significant part of their activities to preparing and studying innovative products or potential technologies. This includes collaborations with other company entities as well as important partnerships with research institutes and universities. Together, the Biraghi Laboratory and the Quality Office form the Biraghi Quality Department, operating under a single Quality Management.